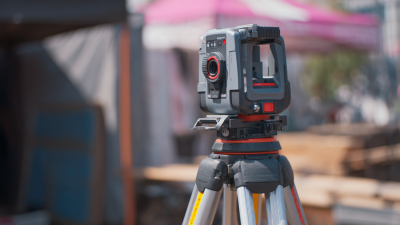
Understanding the Unique Features and Applications of the Best Measuring Equipment for Global Buyers
In the ever-evolving landscape of industrial technology, the demand for precise and reliable Measuring Equipment has become paramount for global buyers seeking to enhance efficiency and accuracy across various applications. According to a recent report by MarketsandMarkets, the global measuring equipment market is projected to reach $20.7 billion by 2025, growing at a CAGR of 6.1%. This growth underscores the critical role of measuring devices in sectors such as manufacturing, construction, and healthcare, where precision is non-negotiable. From digital calipers to advanced laser measuring tools, the diversity of available options reflects the specific needs of different industries. Understanding the unique features and applications of these tools can empower businesses to make informed decisions, optimize operations, and ultimately gain a competitive edge in their respective markets.
Read more »
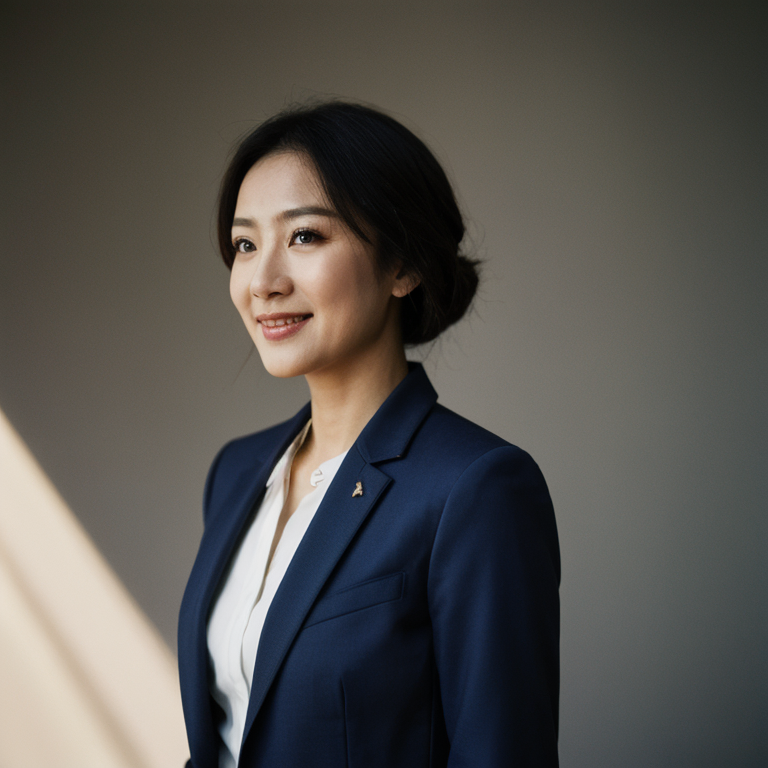
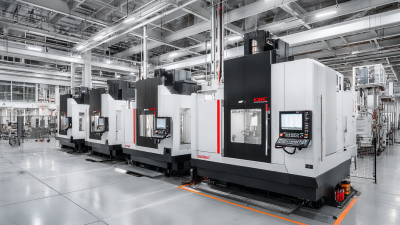
Comprehensive Guide to Different Types of CNC Machining Centers and Their Applications
In today's fast-paced manufacturing landscape, understanding the various types of CNC Machining Centers and their specific applications is crucial for businesses looking to enhance their production capabilities. CNC Machining Centers are sophisticated machines that automate the machining processes, offering precision and efficiency that traditional methods struggle to match. From milling and drilling to turning and grinding, each type of CNC Machining Center serves distinct purposes, catering to diverse industries ranging from aerospace to automotive. This comprehensive guide will explore the different types of CNC Machining Centers, highlighting their unique features, advantages, and the reasons why choosing the right type is essential for optimizing workflows and achieving quality outputs. Whether you are a seasoned engineer or a newcomer to the manufacturing realm, gaining insights into these advanced machines will empower you to make informed decisions that align with your production goals.
Read more »
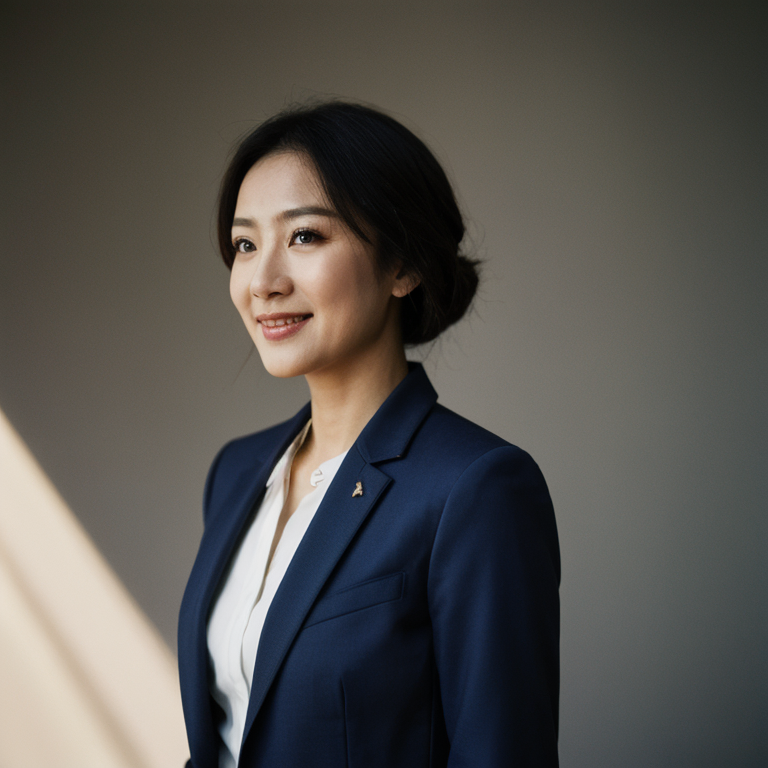
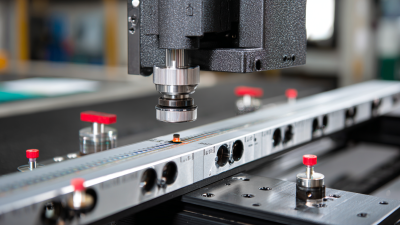
Global Excellence in Manufacturing with Chinese Quality the Best Coordinate Measuring Machine
In the competitive landscape of manufacturing, the significance of precision and quality cannot be overstated, particularly when it comes to the use of Coordinate Measuring Machines (CMMs). According to a recent market report by Research and Markets, the global CMM market is projected to reach $2.7 billion by 2026, driven by the increasing demand for high-quality measurement solutions in sectors such as aerospace, automotive, and industrial manufacturing. The rise of Chinese manufacturing capabilities has been instrumental in shaping this landscape, offering cost-effective yet high-quality alternative solutions. This blog will delve into a comparative analysis of different CMM technologies, emphasizing how Chinese manufacturers have emerged as leaders by balancing quality and innovation, thus solidifying their position in the global manufacturing excellence narrative.
Read more »
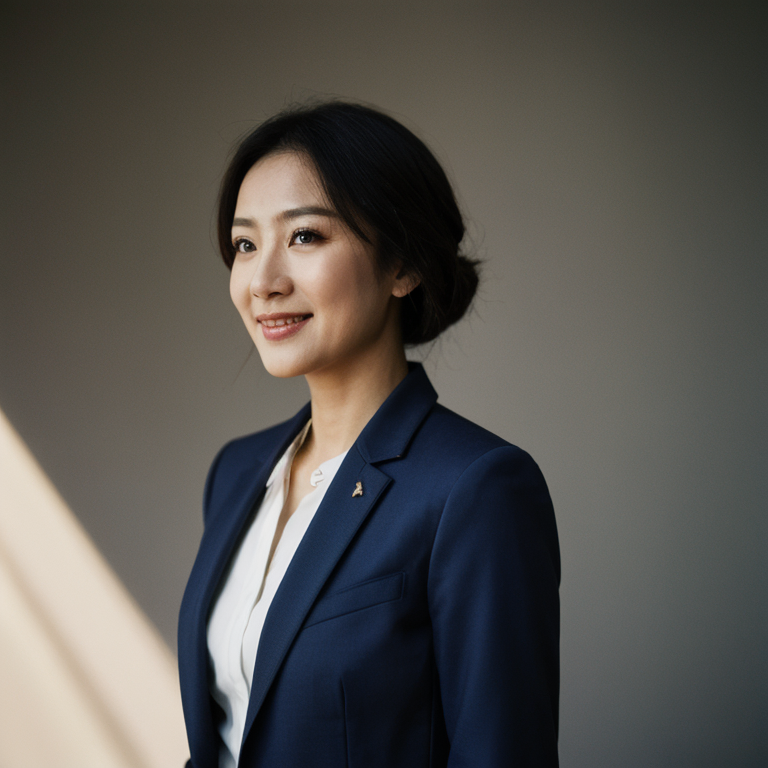
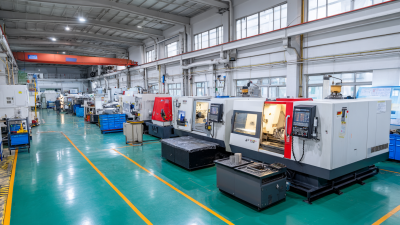
Ultimate Guide to Finding the Best Used Machine Tools for Your Business Needs
In today’s competitive manufacturing landscape, the use of "Used Machine Tools" has become a pivotal strategy for businesses looking to optimize costs and enhance productivity. According to a report by MarketsandMarkets, the global machine tool market is projected to reach USD 88.6 billion by 2025, with the used segment gaining significant traction as industries seek affordable yet high-quality equipment. Companies are increasingly aware that acquiring used machinery not only reduces capital expenditure but also contributes to sustainable practices by extending the lifecycle of existing tools. However, selecting the right used machine tools requires careful consideration of detailed technical specifications to ensure they meet specific business needs. This ultimate guide aims to provide essential insights into evaluating used machine tools, enabling businesses to make informed decisions that align with their operational goals and enhance overall efficiency.
Read more »
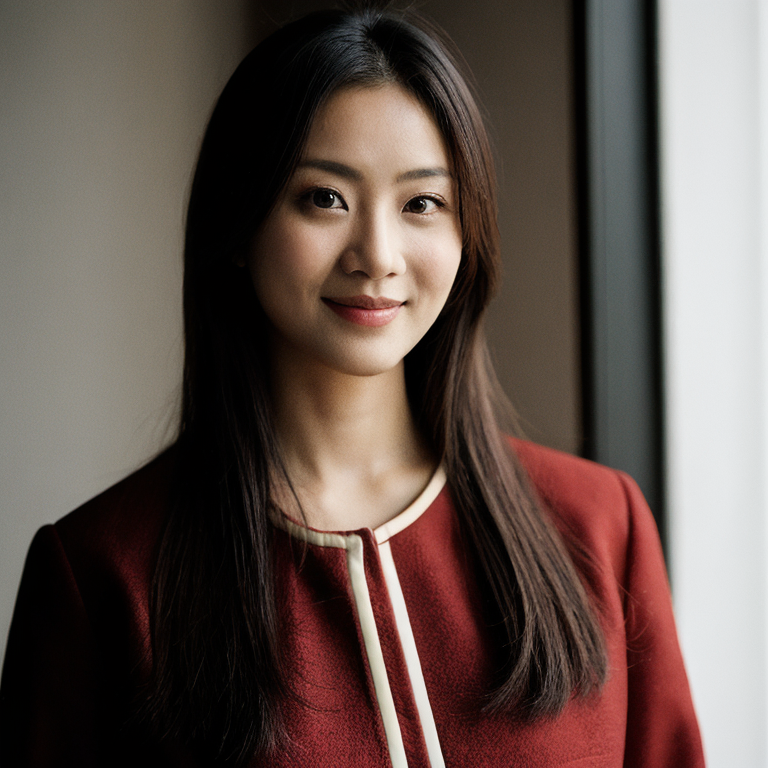
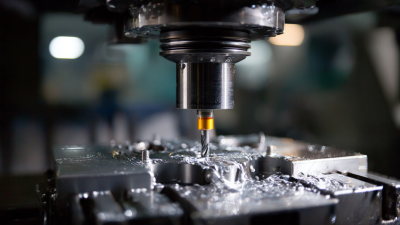
Unlocking Precision in Manufacturing with Best Cnc Machine Tools Comprehensive Technical Specs and Usage Guide
As the manufacturing landscape continues to evolve, the role of CNC (Computer Numerical Control) machine tools has become increasingly critical for achieving precision and efficiency in production processes. According to a report by MarketsandMarkets, the global CNC machine tools market is expected to reach $118.6 billion by 2026, growing at a CAGR of 6.9% from 2021. This growth is driven by the increasing demand for high-quality, complex components across various industries, including aerospace, automotive, and electronics. The integration of advanced technologies such as automation and smart manufacturing is transforming the capabilities of CNC machine tools, allowing manufacturers to optimize their operations and enhance product quality. In this blog, we will delve into the comprehensive technical specifications and usage guidelines of the best CNC machine tools available, unlocking the potential for precision in modern manufacturing.
Read more »
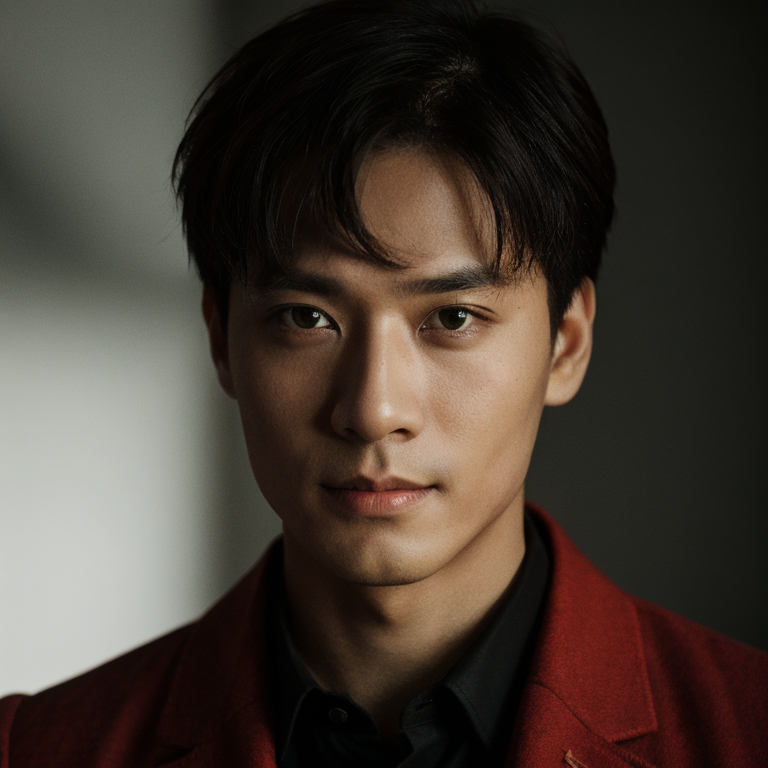
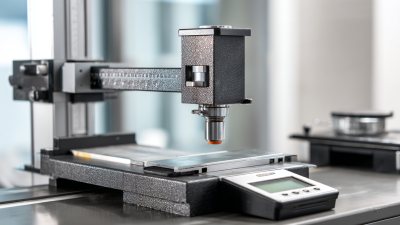
Top Strategies for Selecting the Best Measuring Equipment for Your Business
In today's competitive landscape, selecting the right measuring equipment is crucial for businesses aiming to uphold quality and precision in their operations. As highlighted in the 2022 Global Measuring Equipment Market report, the market is anticipated to reach a value of $30 billion by 2027, driven by increased demand for accurate measuring solutions across various industries. This growth reflects the industry's shift towards adopting advanced technologies that enhance quality control, particularly in manufacturing sectors. With China positioning itself as a leader in manufacturing excellence—earned through a commitment to quality—investing in state-of-the-art measuring equipment is vital for companies seeking to win global respect. By carefully choosing the appropriate tools, businesses can optimize their processes, ensure compliance with international standards, and ultimately, bolster their reputation in the market.
Read more »
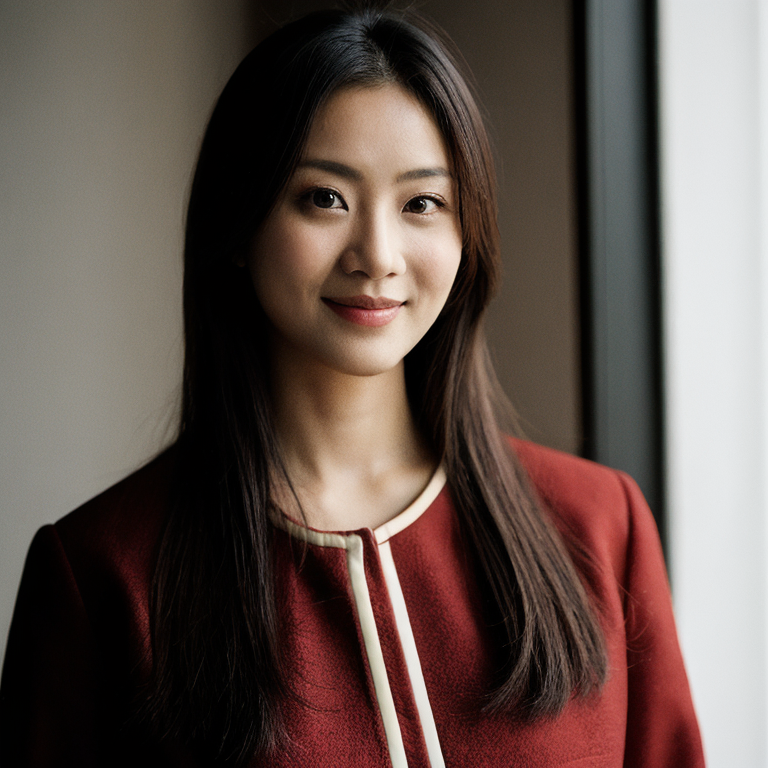
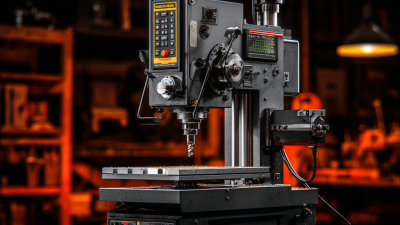
How to Choose the Best Milling Equipment for Your Business in the 2025 Global Market
As we approach the global market landscape of 2025, the milling equipment sector stands at the forefront of technological advancement and economic opportunity. According to a recent report by Markets and Markets, the global milling equipment market is projected to reach $8.5 billion by 2025, growing at a CAGR of 6.3% from 2020. This upward trajectory is driven by increasing demand for processed food products and the continuous expansion of the agricultural sector, particularly in emerging economies. Chinese manufacturers, known for their innovative designs and cutting-edge technology, have established a substantial footprint worldwide, exporting their milling solutions to a diverse range of industries. As businesses navigate this competitive environment, selecting the right milling equipment becomes crucial for ensuring efficiency, cost-effectiveness, and sustainability.
Read more »
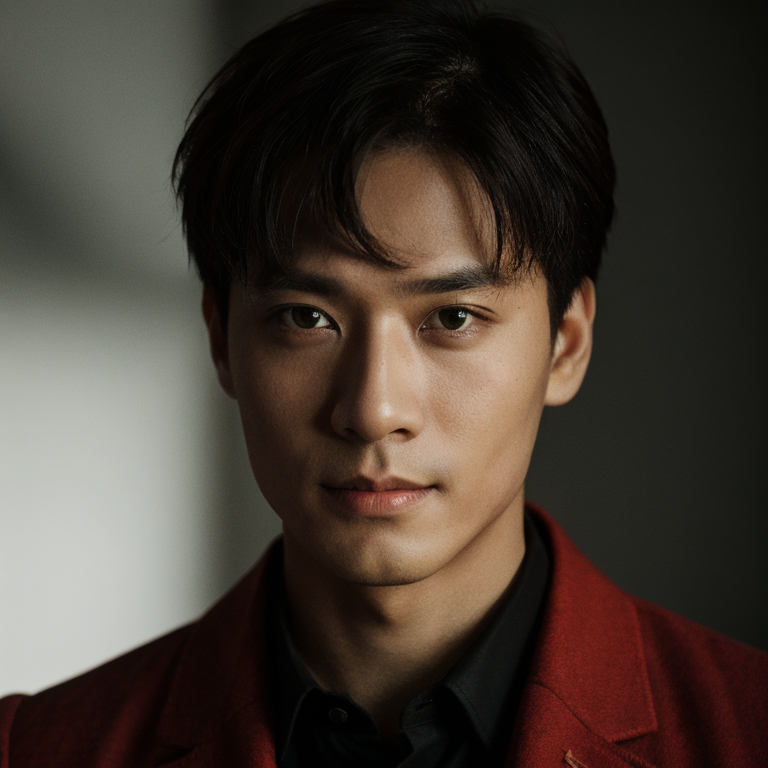
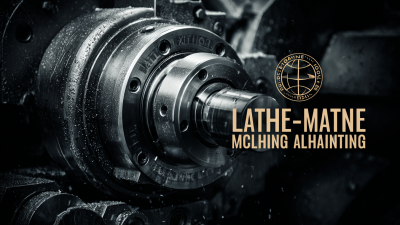
Leading Global Manufacturer of The Best Lathe and Milling Machines for Export
In today's highly competitive manufacturing landscape, the significance of precision engineering cannot be overstated. At the forefront of this innovation are lathe and milling machines, essential tools that empower manufacturers to achieve unparalleled accuracy and efficiency in their production processes. This guide will explore the world of lathe and milling machines, highlighting the leading global manufacturers that are setting industry standards and driving advancements in technology. Whether you are a seasoned professional in the machining industry or a newcomer eager to delve into manufacturing, understanding the capabilities and advantages of these machines is crucial. From optimizing workflow to enhancing product quality, this blog aims to provide valuable insights into selecting the best lathe and milling machines for export, ensuring that you make informed decisions for your business or projects.
Read more »
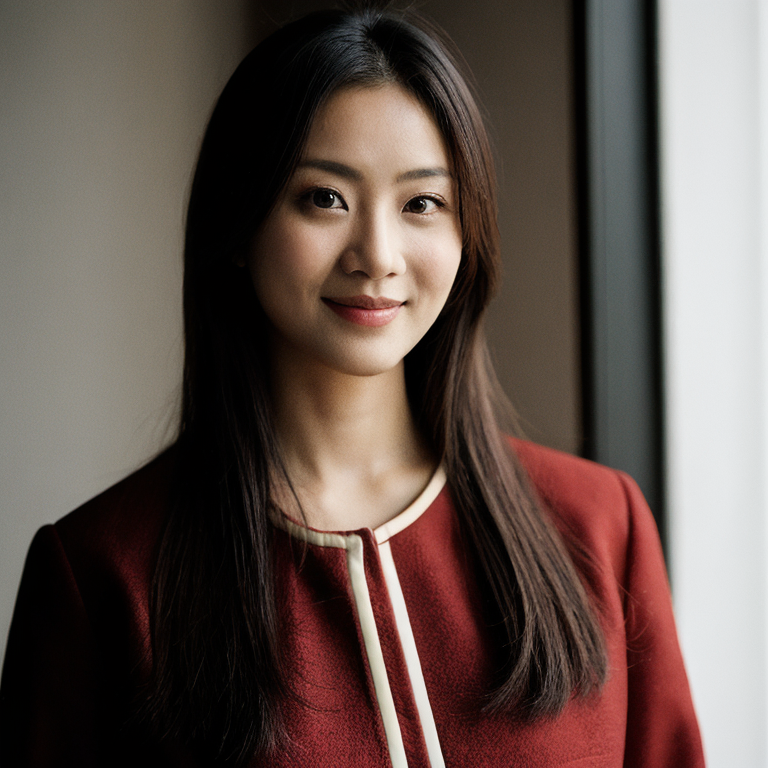
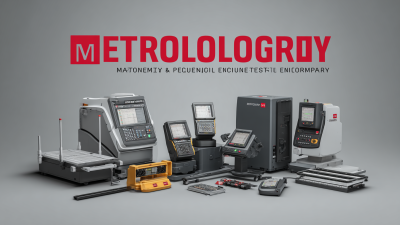
Mastering Precision: Your Ultimate Guide to Selecting the Best Metrology Equipment for Global Procurement
In today's rapidly evolving global marketplace, the importance of precise measurements cannot be overstated, making the selection of high-quality Metrology Equipment a critical factor for success. According to a recent report by Grand View Research, the global metrology equipment market is expected to reach USD 17.45 billion by 2027, with a compound annual growth rate (CAGR) of 6.2% from 2020 to 2027. This growth underscores the increasing reliance of industries such as manufacturing, aerospace, and automotive on advanced metrology solutions to ensure product quality and regulatory compliance. As companies expand their operations internationally, understanding the nuances of metrology equipment becomes essential for maintaining competitiveness, optimizing quality assurance processes, and reducing operational costs. This guide aims to provide you with crucial insights and best practices for selecting the most appropriate metrology equipment tailored to your specific global procurement needs.
Read more »
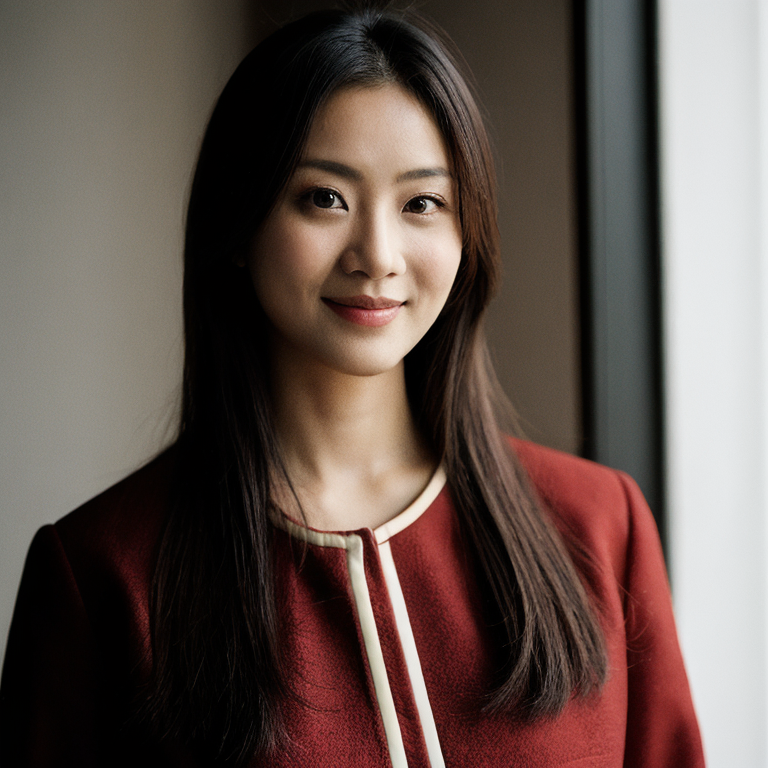
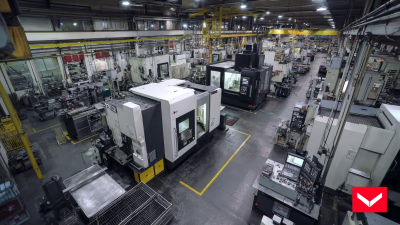
Precision Craftsmanship: Elevating Global Industries with China's Best Used Machine Tools
In the rapidly evolving landscape of global manufacturing, precision craftsmanship is becoming increasingly critical for driving innovation and efficiency. According to a recent report by MarketsandMarkets, the global market for used machine tools is projected to reach approximately $7.76 billion by 2025, growing at a CAGR of 3.5% from 2020. This surge is attributed to the rising demand for cost-effective manufacturing solutions in various sectors, including automotive, aerospace, and electronics. China's robust market for used machine tools offers a wealth of opportunities for industries seeking high-quality, reliable equipment without the financial burden of new purchases. By leveraging these precision-engineered tools, companies can not only enhance production efficiencies but also significantly reduce operational costs, ultimately contributing to improved competitiveness on a global scale.
Read more »
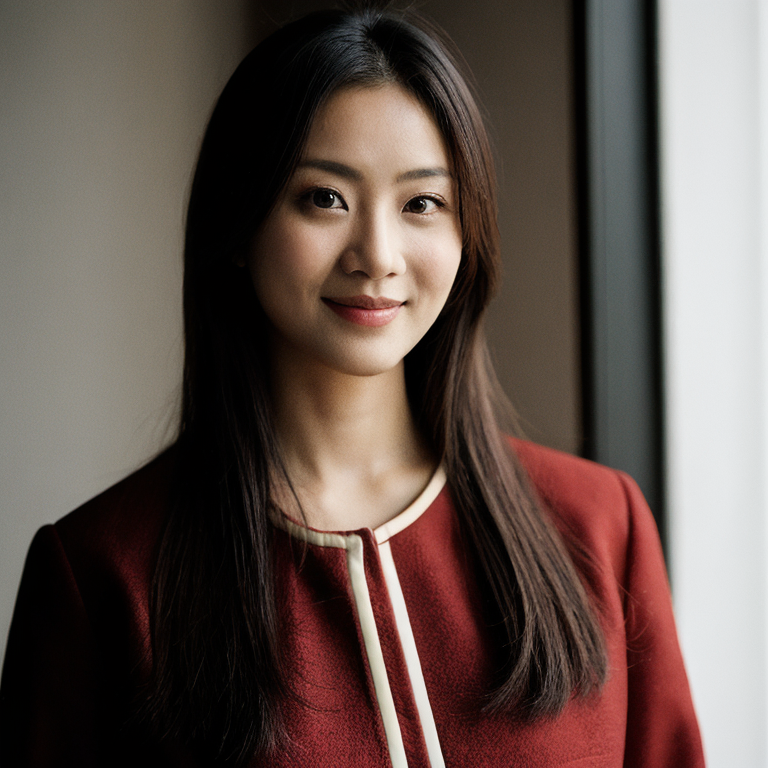
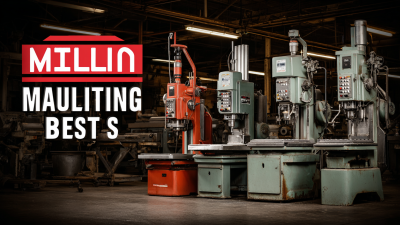
5 Proven Best Milling Equipment Options for Your Manufacturing Needs
In the dynamic world of manufacturing, choosing the right Milling Equipment is essential for optimizing production efficiency and ensuring product quality. With a plethora of options available in the market, it can be overwhelming for manufacturers to identify the best machinery suited for their specific needs. This guide aims to demystify the selection process by presenting five proven milling equipment options that cater to various manufacturing requirements. By understanding the fundamental differences and unique features of these milling machines, manufacturers can make informed decisions that enhance their operational capabilities. Whether you are a small business looking to scale up or a large enterprise aiming for precision, mastering the ins and outs of milling equipment will empower you to boost productivity and achieve your manufacturing goals.
Read more »
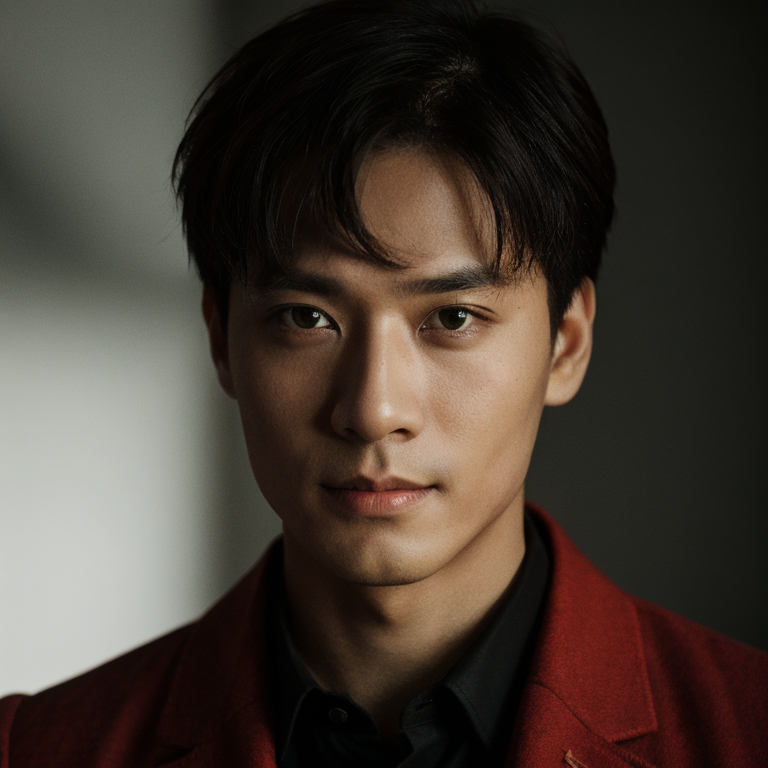
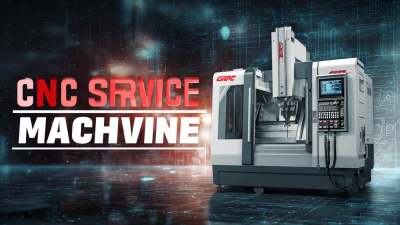
Unveiling the Secrets to Finding Quality Suppliers for Best CNC Machine Service
In today's highly competitive manufacturing landscape, the demand for high-quality CNC machine service is paramount. According to a recent industry report by Grand View Research, the global CNC machine market size is expected to reach $100 billion by 2025, growing at a CAGR of 6.2%. This rise is indicative of the increasing reliance on precision engineering and customization in various sectors, including aerospace, automotive, and medical devices. However, sourcing reliable suppliers for CNC machine services can often feel overwhelming. With numerous options available, identifying the ones that consistently deliver quality can be challenging. This guide aims to unveil the secrets behind finding top-tier suppliers, ensuring that your CNC machining needs are met with precision and efficiency, thus enhancing your operational capabilities and overall business success.
Read more »
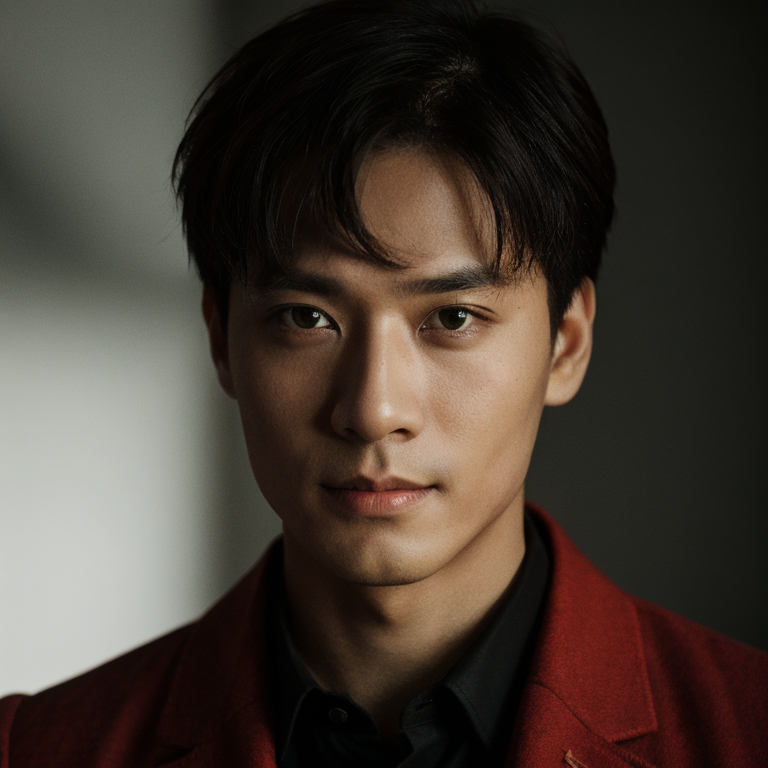
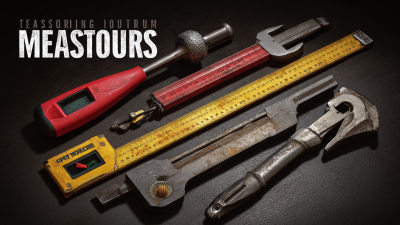
How to Choose the Best Measuring Tools for Accurate Results in Your Projects
In today's rapidly evolving landscape, the importance of accurate measurements in project execution cannot be overstated. According to a recent report by the National Institute of Standards and Technology, nearly 70% of project failures can be traced back to inadequate measurement tools and techniques. As industries increasingly rely on precision for success, choosing the right Measuring Tools becomes paramount. Whether you are in construction, manufacturing, or any engineering field, the tools you select can greatly influence the quality of your outcomes. As we delve into the future of Measuring Tools, it is crucial to understand how advancements in technology are shaping their development, ensuring not just accuracy but also efficiency in achieving project goals. By equipping yourself with the best measuring instruments, you position your projects for success and sustainability in a competitive market.
Read more »
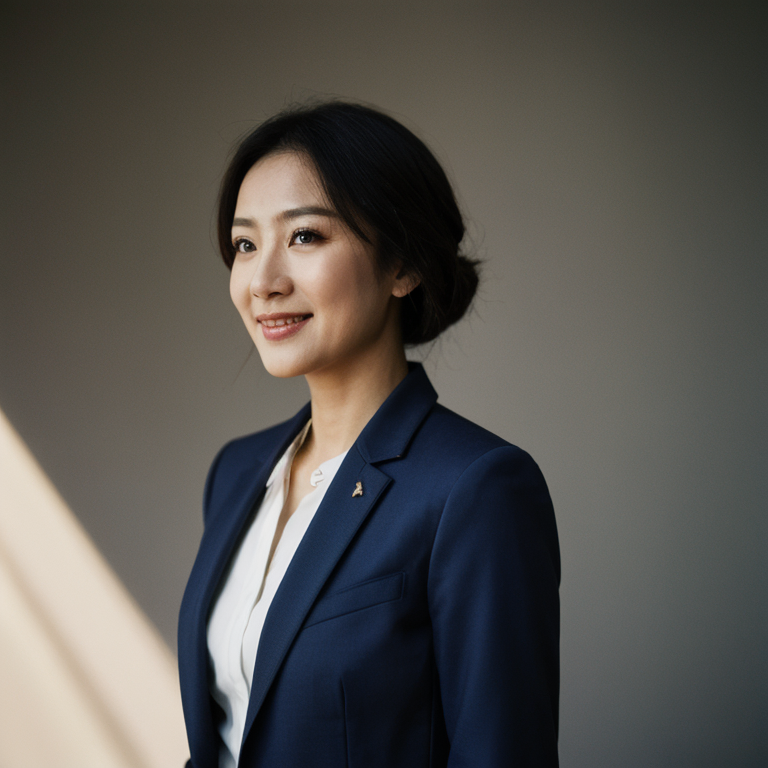
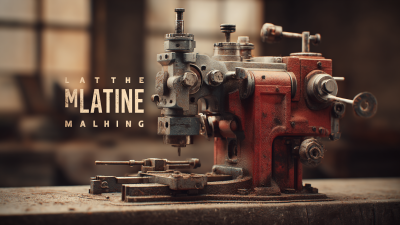
Exploring Unique Alternatives to the Best Lathe and Milling Machine Options
In the ever-evolving world of machining and manufacturing, the quest for the best lathe and milling machine options continues to captivate professionals and enthusiasts alike. As we dive into 2025 industry trends, it's essential to explore not only the conventional choices but also the innovative alternatives that are emerging in the market. This blog will highlight unique options that challenge traditional boundaries, offering insights into the latest advancements in technology and design. By examining these alternatives, we aim to provide a comprehensive understanding of how they can enhance efficiency and precision in various applications, ultimately empowering machinists to make informed decisions tailored to their specific needs. Join us as we embark on this exploration of distinctive lathe and milling machine solutions that could redefine your machining experience.
Read more »
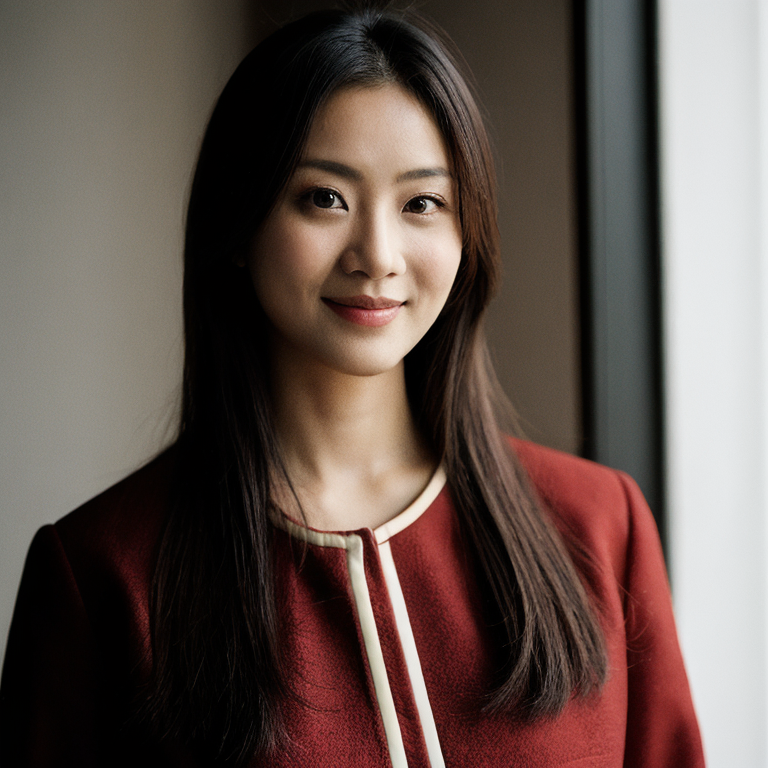
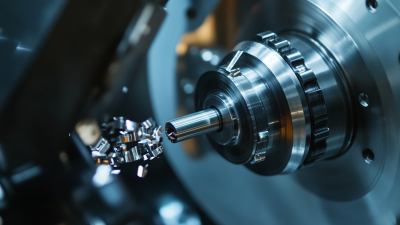
Crafted Precision Global Reach of Best Cnc Machine Tools from China
In the fast-evolving landscape of manufacturing, CNC machine tools have become indispensable for precision engineering across diverse industries. According to a report by MarketsandMarkets, the global CNC machine tools market is expected to grow from USD 80.8 billion in 2020 to USD 97.1 billion by 2025, reflecting a compound annual growth rate (CAGR) of 4.0%. This growth is largely driven by the increasing demand for automation and the need for high-quality manufacturing processes. As businesses seek to optimize productivity and maintain competitive edges, finding reliable suppliers of high-quality CNC machine tools is vital. In this ultimate guide, we will explore effective strategies for identifying top-tier suppliers from China, a leading hub for CNC machine tools, ensuring that manufacturers can leverage precision and innovation while meeting global market demands.
Read more »
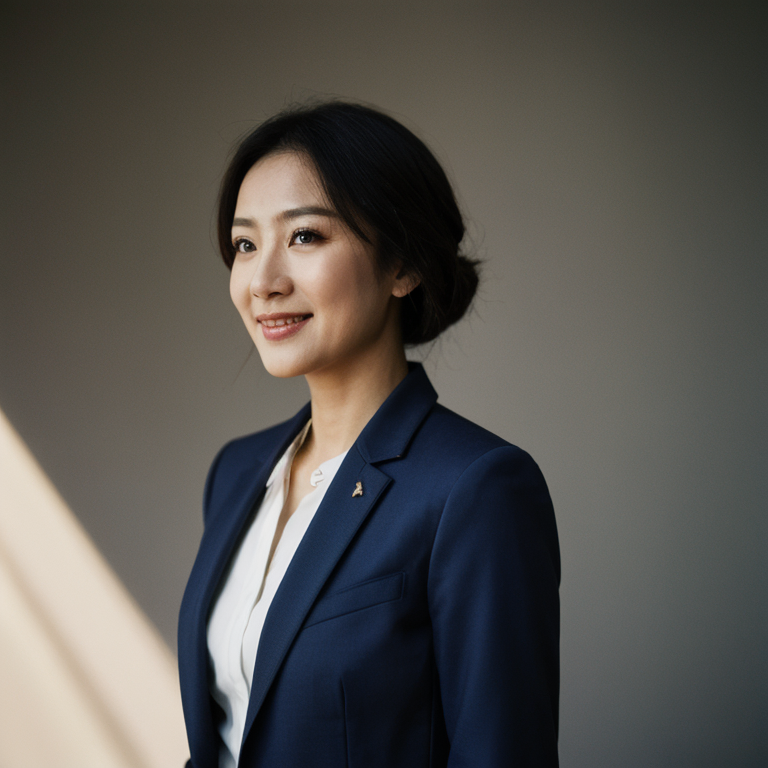